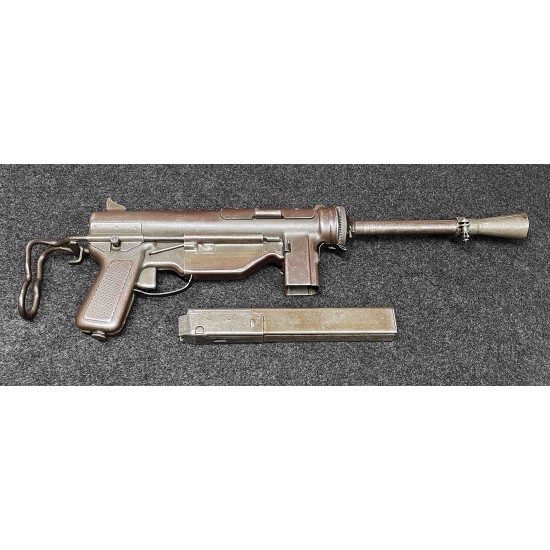
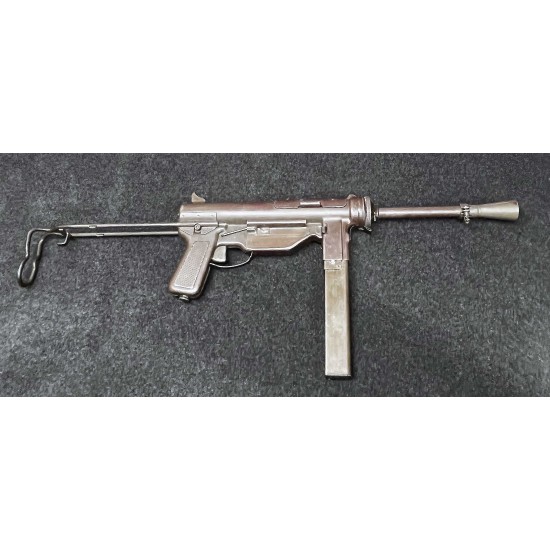
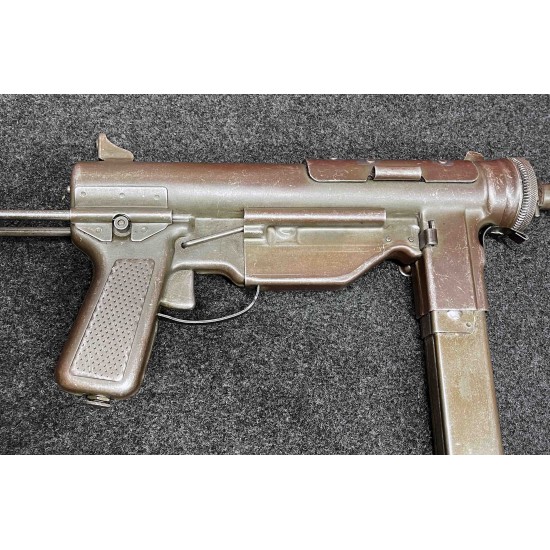
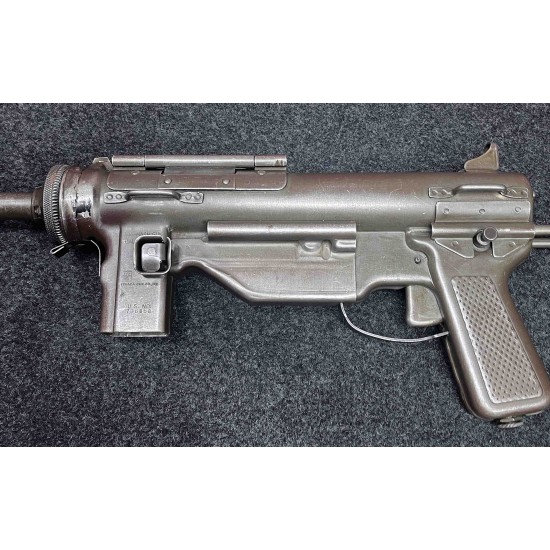
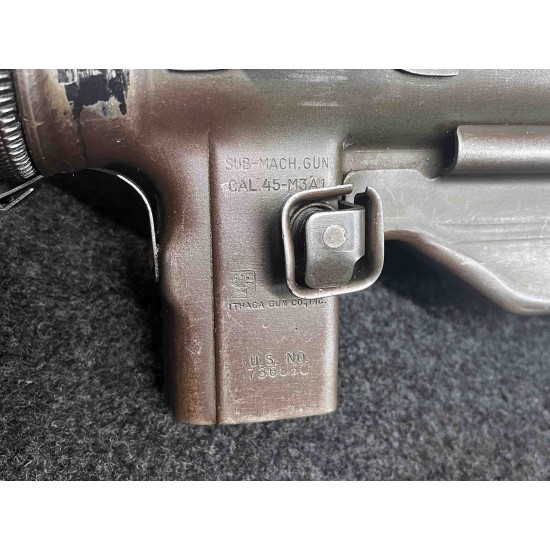
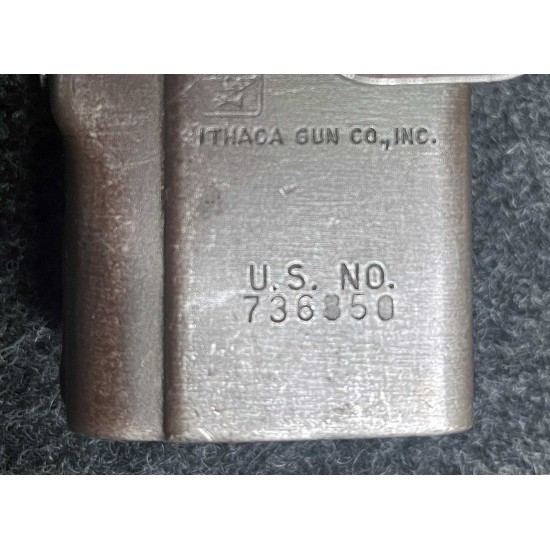
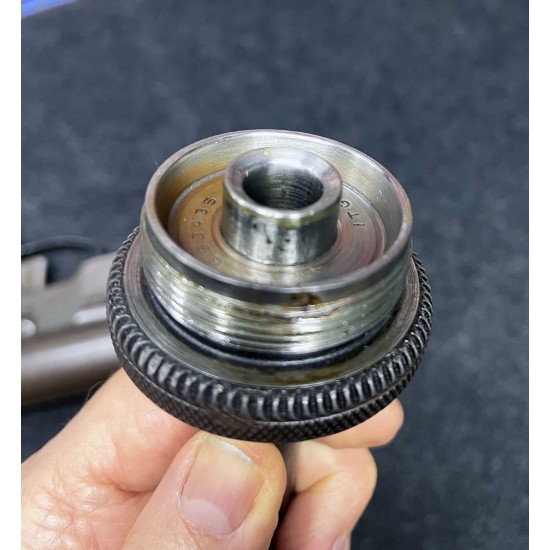
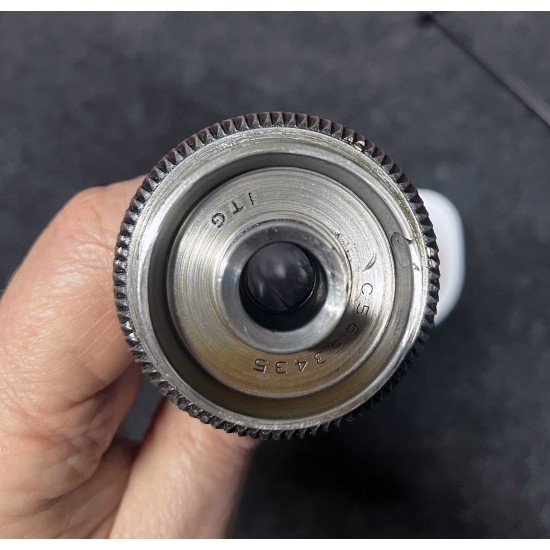
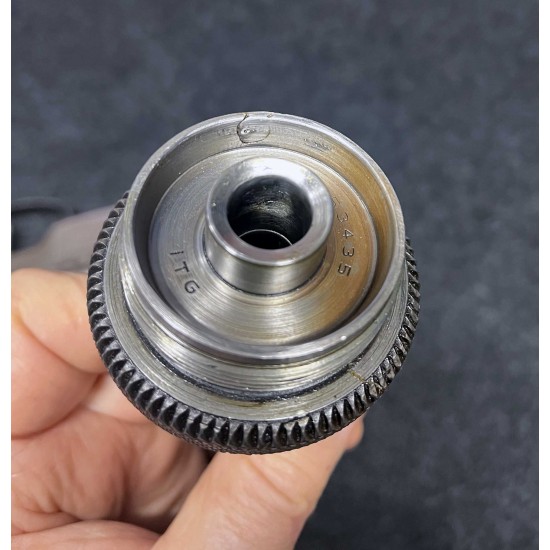









M3A1 WWII/Korean War Grease Gun 45ACP Ithica Arms Manufacture #736850 one serialized 250-A 30RND magazine. This gun had a hole drilled through the chamber 50 years ago and has since been retig welded . We have test fired this for a few hundred rounds and works fantastic. Many guns had this done to get them out of certain countries.
The M3 is an American .45-caliber submachine gun adopted for the U.S. Army service on 12 December 1942, as the United States Submachine Gun, Cal. .45, M3.[12] The M3 was chambered for the same .45 ACP round fired by the Thompson submachine gun, but was cheaper to produce and lighter, although, contrary to popular belief, it was less accurate.[12] The M3 was commonly referred to as the "Grease Gun" or simply "the Greaser", owing to its visual similarity to the mechanic's tool.[13]
The M3 was intended as a replacement for the Thompson, and began to enter frontline service in mid-1944. The M3A1 variant was used in the Korean War and later conflicts.
The M3 and M3A1 were largely withdrawn from U.S. frontline service beginning in 1959, but continued to be issued until at least the 1991 Gulf War as equipment aboard armored vehicles, in particular the M60 tank (which was used by some United States National Guard units until 1997).[24]
M3A1[edit]
In December 1944, a modernized version of the M3 known as the M3A1 was introduced into service, with all parts except the bolt, housing assembly, and receiver interchangeable with those of the M3. The M3A1 had several improvements:
- Most significantly eliminating the troublesome crank-type cocking lever assembly, replaced by a recessed cocking slot machined into the top front portion of the bolt, letting it be cocked by putting a finger into the cocking slot and pulling back the bolt.
- The retracting pawl notch was removed, and a clearance slot for the cover hinge rivets was added.
- The ejection port and its cover were lengthened to allow the bolt to be drawn back far enough to be engaged by the sear.
- The safety lock was moved further to the rear on the cover.
- To make loading the single-feed magazine easier, a magazine loading tool was welded to the wire stock; it also served as a cleaning rod stop.
- The barrel bushing received two flat cuts that helped in barrel removal by using the stock as a wrench.
- The barrel ratchet was redesigned to provide a longer depressing lever for easier disengagement from the barrel collar.
- The spare lubricant clip (on the left side of the cocking lever assembly) was removed, replaced with an oil reservoir and an oiler in the pistol grip of the receiver assembly. The stylus on the oiler cap could also double as a drift to remove the extractor pin.
At 7.95 pounds empty, the M3A1 was slightly lighter than the M3, at 8.15 pounds empty, primarily due to the simplified cocking mechanism.[12] The M3A1 was formally approved for production on 21 December 1944.[12]
The M3A1 modifications resulted in a more reliable, lighter weight, easier to maintain, and easier to field strip submachine gun; the original M3 needed both the trigger guard removed and the cocking crank assembly detached from the receiver housing before unscrewing the barrel, but the M3A1 only required the user unscrew the barrel. To date, only one 9 mm conversion kit for the M3A1 has been discovered.[15]
Because it had already been issued in large numbers, the existing M3 magazine design was retained, despite demonstrated deficiencies exposed during the weapon's firing trials and its early combat service.[31] In an effort to improve reliability, a hard plastic Tenite cap designated T2 was adopted in November 1944 to fit over the feed lips of loaded magazines.[32] These caps protected the feed lips while keeping out dirt, sand, and debris.[34] Sometime during the 1960s the hard T2 plastic cap was replaced in service with one of pliant neoprene rubber, which could be removed with less noise.[35] Unfortunately, during service in the humid climate of Vietnam it was discovered that the rubber cap caused rust to form on the covered portion of the magazine, while causing loaded ammunition to corrode.[35]
Initially, M3 submachine guns returned for repair were not upgraded to the M3A1 standard, but merely inspected to ensure they had the improved M3 housing assembly and magazine release shield.[36] During the Korean War, existing M3 guns in service were converted to the improved M3A1 configuration using additional new production parts.[37] During the conversion, armorers frequently removed the M3 cocking handle, leaving the rest of the now-redundant cocking mechanism inside the subframe.[38] Overall, the M3A1 was seen by most soldiers and Ordnance technicians as an improvement over the M3. However, complaints of accidental discharge continued to occur even as late as the Korean War.[38] These incidents were sometimes caused by dropping the weapon on a hard surface with an impact sufficient to knock open the ejection port cover and propel the bolt backwards (but not enough to catch the sear). The return springs would then propel the bolt forward to pick up a cartridge from the magazine and carry it into the chamber, where the bolt's fixed firing pin struck the primer upon contact.[38][39]
In 1945, the Guide Lamp factory manufactured 15,469 M3A1 submachine guns before production contracts were canceled with the end of the war. During the Korean War, Ithaca Gun Co built another 33,200 complete guns as well as manufacturing thousands of parts for the repair and rebuilding of existing M3 and M3A1 weapons.[40]
- Stock: 1
- Model: M3A1 WWII/Korean War Grease Gun 45ACP
- Weight: 3.60kg